Rail Infrastructure Manufacturer
Results
- 43 business processes mapped in their entirety with 28 different process owners from 12 different functional departments across the business
- 160 problems and opportunities documented and analysed to identify the 35 highest priority improvement actions
- Roadmap developed for longer-term business transformation (with readiness to support migration for new ERP system upgrade)
- Senior Leadership Team’s improved alignment around how and where to focus attention and resources to enable them to realise the biggest benefits to improve efficiency and profitability
- Accountability and responsibility for each process was clarified and agreed
- Process purpose and definitions documented to enable understanding of what value is being created as a result of each process being carried out
Overview
OBC Lean Solutions mapped the 43 most important business processes across 12 different functional departments and identified 160 different problems and improvement opportunities with those processes. We then analysed those problems and opportunities by ranking them by improvement impact and required effort to create a number of options for short-term improvements and those for a longer-term business transformation.
Our Team were tasked to liaise with all of the individuals from all of the functional departments who were deemed to be responsible for the most important processes. We then mapped those processes to understand and visualise how employees were currently executing those processes, critically evaluating the effectiveness and efficiency of each process with the respective process owners.
For each process, we created and documented a process purpose and definition, identified the roles in the organisation that were responsible and accountable for each process and reviewed the process performance measures for suitability & effectiveness. We investigated how the process partners in different functional areas understood the same processes that involved multiple functional departments to determine how aligned they were.
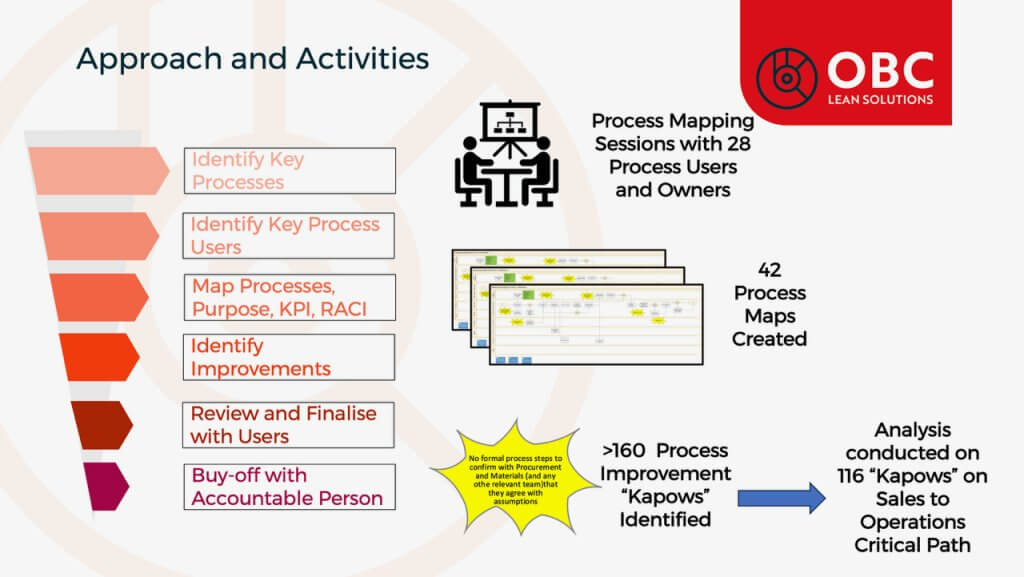
We were able to identify process steps that were inhibiting the smooth flow of product and information through their processes (those causing inefficiencies), we identified the origins of both process and transactional defects and we made process change recommendations to reduce work that was not deemed to be creating any value for the business.
Cause and effect analysis was conducted using an interrelationship digraph to prioritise improvements and identify drivers and outcomes to develop the elements required to provide a workable business transformation roadmap.
Regular reporting and a final report out to the Senior Leadership Team enabled the Leadership Team to become more aligned about how and what must focus their time and attention on going forward to help them better achieve their goals.
Observations
The client was looking to improve the profitability of their business by improving processes to enable increased efficiencies. Some minor organisational changes had recently been made and the business was in the formative planning stages for a large business transformation programme that included the upgrading of their ERP system.
Objectives
OBC Lean were asked to evaluate and assess how visible and effective the business processes were throughout the business, provide recommendations to improve them in the short-term and long-term and create a roadmap for their business transformation to enable the business to become more efficient and profitable.
This assignment was the first phase of a multi-year transformation to help align and inform the senior leadership team about the opportunities that are available to them for improving efficiencies, process quality and process performance.
Actions
By using a collaborative approach with all process owners, functional departmental leads and the senior leadership team, we were able to identify process failures and weaknesses and recommend specific process improvement opportunities at both an operational and strategic level.
As a result of our investment in regular and ongoing communication with the Senior Leadership Team we were able to improve the Senior Leadership Team’s alignment on the strategies and activities that they will focus on as part of their business transformation.
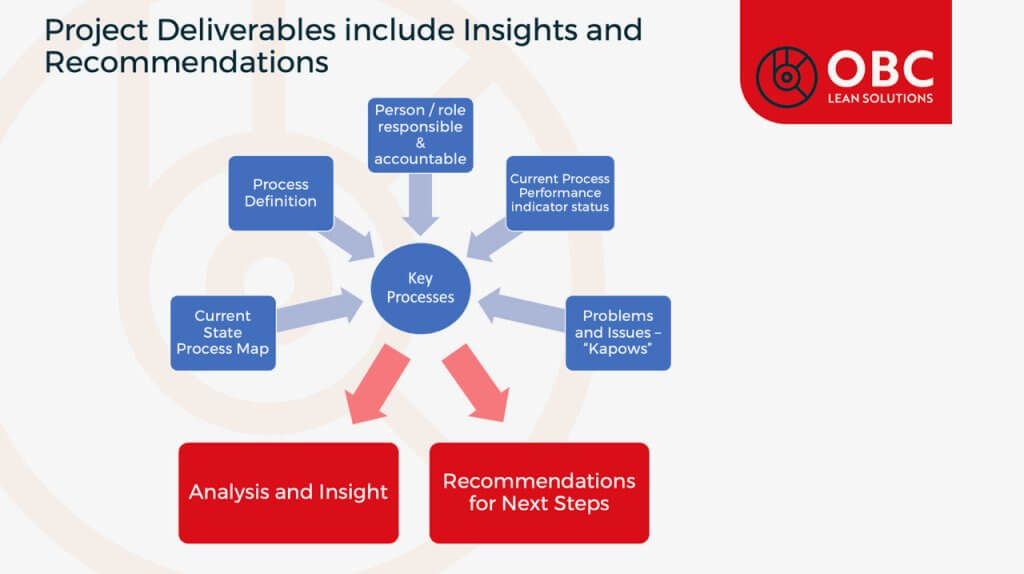