
How to Improve Responsiveness & Agility in High-Mix Low-Volume (HMLV) Manufacturing
Why is High-Mix Low Volume Manufacturing Different and Unique?
A high-volume manufacturer producing a range of standard components will have a stable and predictable demand (seasonally adjusted), which often can be forecasted relatively easily. It will probably have a small supply-base providing standard ship-to-stock parts and materials. High volumes can be leveraged to reduce the ordering frequency and subsequently run a more efficient supply chain operation with moderate to high inventory turns and little exposure to excess and obsolete inventory.
The opportunities for identifying waste in these processes can often be realised across a number of products, part families or processes so the benefits associated with one improvement action can often benefit many times over.
What are the Challenges for High-Mix Low-Volume Manufacturers?
High-mix low-volume (HMLV) manufacturers often endure a high degree of demand volatility and variability, so they require much more complex supply chain processes, process sequences, schedules, routings and forecasts etc. It is the complexities associated with these activities that constrain the smooth flow of materials through manufacturing and the entire value-chain, as product forecasts continually change in line with changing demands. HMLV manufacturers have a relatively larger supplier base, each providing many unique components for specialised products with different lead times, making the supply base and internal operations management more complex.
From a quality perspective, when seeking to improving process capability and eliminate defects, the lower the volume of product being processed, the fewer the number of opportunities there will be to fully optimise the process in a cost-effective manner because the number of times the benefits can be realised is limited.
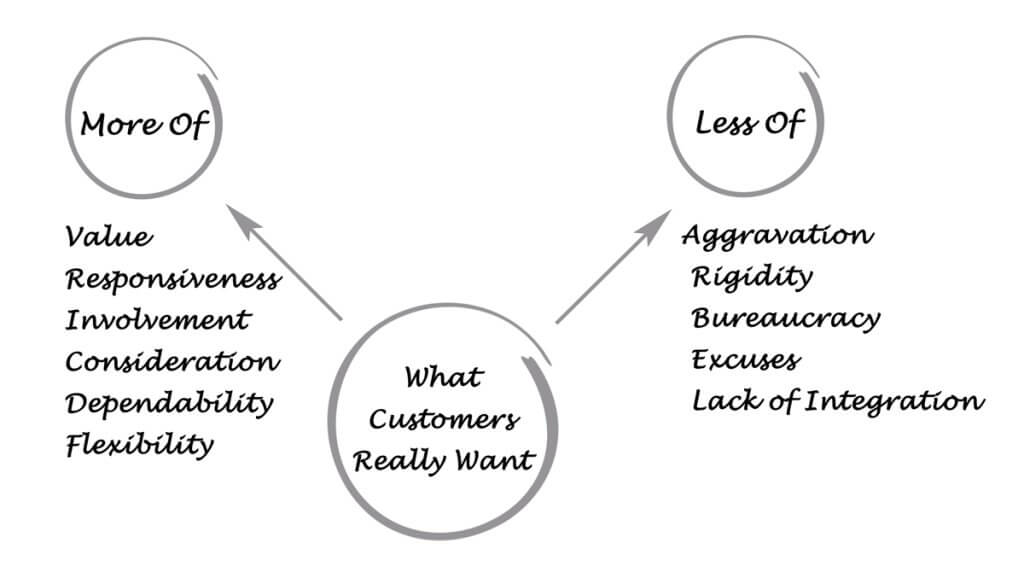
What are the Opportunities for High-Mix Low-Volume Manufacturers?
To improve and optimise flow throughout the wider value chain of a HMLV manufacturer, the physical flow of material, part routings and process sequences need to be visible, defined and better understood in order for people to identify where and what the issues are that are constraining the achievement of their performance targets.
Processes need to be predictable and capable; forecasting, scheduling and planning processes are critical for driving improvements. Performance needs to be visible within operations (at a machine, line and facility level) and regularly reviewed by effective leaders at all levels who are accountable for performance.
In addition, there will be a significant amount of value opportunity derived from the performance of the supply chain, hence the need to have effective and transparent measures in place for inventory turns, inventory accuracy, forecast accuracy, material availability, supply chain costs and shipping performance etc.
It will be vital to have in place effective processes such as S&OP, forecasting, material planning and scheduling etc. With these in place as a baseline, opportunities to improve performance will become visible through the use of site level material flow path maps, clearly defined replenishment strategies, a “Plan for Every Part (PFEP)” and a long-term supply chain improvement plan.
For HMLV manufacturers, having the edge on the competition is less about product differentiation, product quality and manufacturing performance and more about competitive pricing, perceived value and response times which are influenced by both the Supply Chain and Operations together.
An Alternative Approach for Improving Operations & Supply Chain
A high-volume manufacturer producing a range of standard components will have a stable and predictable demand (seasonally adjusted), which often can be forecasted relatively easily. It will probably have a small supply-base providing standard ship-to-stock parts and materials. High volumes can be leveraged to reduce the ordering frequency and subsequently run a more efficient supply chain operation with moderate to high inventory turns and little exposure to excess and obsolete inventory.
The opportunities for identifying waste in these processes can often be realised across a number of products, part families or processes so the benefits associated with one improvement action can often benefit many times over.
What are the Challenges for High-Mix Low-Volume Manufacturers?
High-mix low-volume (HMLV) manufacturers often endure a high degree of demand volatility and variability, so they require much more complex supply chain processes, process sequences, schedules, routings and forecasts etc. It is the complexities associated with these activities that constrain the smooth flow of materials through manufacturing and the entire value-chain, as product forecasts continually change in line with changing demands. HMLV manufacturers have a relatively larger supplier base, each providing many unique components for specialised products with different lead times, making the supply base and internal operations management more complex.
From a quality perspective, when seeking to improving process capability and eliminate defects, the lower the volume of product being processed, the fewer the number of opportunities there will be to fully optimise the process in a cost-effective manner because the number of times the benefits can be realised is limited.