
Want to Beat the Competition? Take a Look at How You Measure Your Company’s Supply Chain Performance
The Importance of Supply Chain Performance for Manufacturers
You get the dreaded call from your most important customer asking where the order is that they should have received from you that very morning.
On investigation, your Supply Chain Manager confirms that “the order wasn’t scheduled because they were short of components, they didn’t forecast enough stock and it also looks like the inventory on the stock system is wrong, oh, and the Material Scheduler is on holiday this week”. It’s a weak explanation isn’t it – but it’s the sort of reason I hear quite often.
To resolve the immediate situation, you order stock, courier it at premium cost, ask your staff to work overtime and book an additional courier to ship the order that night. Sounds like a result? Maybe. But although you pulled out all of the stops to get the order to the customer as soon as you discovered the problem, it cost you money, negatively impacted your profit, credibility and reliability, and unnecessarily consumed a lot of your team’s time.
As a High-Mix Low-Volume (HMLV) manufacturer, what’s the most important factor in setting you apart from the competition?
For many HMLV companies it’s not your manufacturing competencies, but the performance of your overall end-to-end supply chain.
With supply chain performance now often becoming the differentiator between manufacturers producing similar products, I find it surprising that many HMLV manufacturers have still not established effective and robust supply chain processes or performance measures. Without these in place how can the leadership team make informed decisions about their opportunities to improve, how much waste exists or how well they are providing maximum value to their customers?
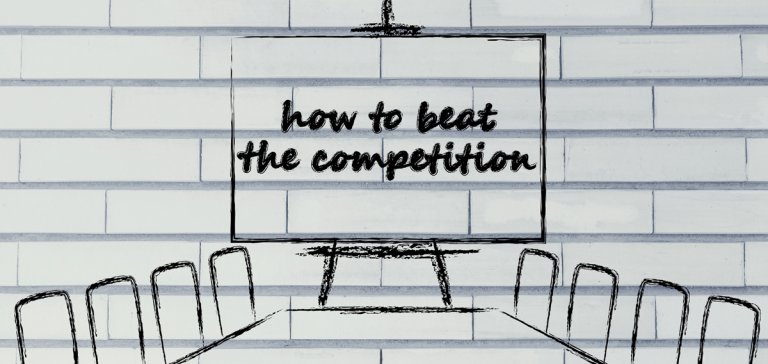
The Benefits of Effective Supply Chain Performance Measures
By focusing efforts on establishing well thought through end-to-end supply chain metrics and internal supply chain oriented metrics, you can enable your team to better understand supply chain performance and increase the focus on taking the right actions to drive improvement. This “balanced” set of supply chain performance measures will inform the leadership team of how well your supply chain is performing over time and align the leadership team on areas and processes that need improving.
By establishing the processes, conducting the right analyses and actively measuring leading indicators of process performance, you can ensure that you will know well in advance (and before your customer) if you will be unable to fulfil an order that you had previously committed to.
Overview of Some Common Supply Chain Performance Measures
There are many Supply Chain Performance Measures that you can put in place to help you monitor, control and direct performance. Your company’s business strategy and management team would be most suited to determining the ones that are most relevant and appropriate for your company.
I have identified and described a number of core supply chain measures below that should be on any HMLV manufacturers dashboard, no matter what:
- Strategic Supply Chain Performance Measures:
- Cash-to-cash cycle time: This is the time between paying for raw materials and components and getting paid for a product. The faster your company can recover its investment in stock and raw materials, the more cash it will have on hand to make and deliver more product and make more money
- Inventory days of supply: This is an easy performance measure to put in place, it is an efficiency ratio that measures the average number of days that inventory is held before it is sold
- Tactical Supply Chain Performance Measures:
- Material spend on ‘Pull”: This is a simple indicator of %age of material spend that is sourced on a pull replenishment basis (as opposed to “push” that is usually planned using an ERP/MRP system)
- Forecast accuracy and forecast variability: Forecasts are not expected to be right but they are useful on an ongoing basis for driving incremental improvements. There is no “acceptable” forecast error, in fact if there is one thing that you can be sure of, forecasts are never right. These measures are about creating the right information that is available to help make informed supply chain decisions
- ABC analysis and part segmentation analysis by replenishment type: Identify the “ABC” class, replenishment type, annual demand and annual demand value to each of your SKUs. Summarise the data by the various categories and use the information to identify opportunities to improve
- Operational Supply Chain Performance Measures:
- %age of component parts mapped by material flowpath: Create a chart or map showing all of the different flow paths that exist for getting your stock parts or components to the location of consumption (the location where the parts are consumed by your assembly process). The intent is to create the map and assign parts to each flow-path, identify opportunities to simplify and improve flow and then execute the improvements
- Inventory accuracy: This is a measure of the results of regular planned inventory record audits of part numbers, part locations and a count of the parts in the given location. What is audited would be determined by inventory audit schedule, which would typically be based on the physical demand quantity and/or value of part number-location
These “core” Supply Chain Measures will help you establish a balanced view about how well your supply chain is performing. Without these, how else do you know whether your supply chain is creating value for your own business or for your customers?
These measures represent both leading and lagging indicators, making it possible for you to monitor and control internal supply chain and logistical process performance indicators so that minor issues can be discovered and corrected before they cause a major disruption to you or your customer.
Benefits & Implementation Considerations
Effective Supply Chain Measures will teach and inform you and your team about what you are doing well and what needs to improve. They will illustrate the size of the opportunities that are available to you and your team and enable you to make improvements for the benefit of the entire company.
In my experience, start with just a few measures to begin with, the ones that your team think are the most important, and then get them established and clearly defined so all of the team can interpret them and make sense of what they mean. It will be likely that the metrics enlighten the leadership team and align them to focus on different aspects of performance that they hadn’t previously considered or had processes in place to measure.
Once the team have gone through the process of reviewing the performance measures and agreeing actions to improve them a few times, they should recognise their benefits and be more receptive to introducing other additional measures to further inform all levels of the organisation of different process performance characteristics. These will integrate with your strategy and policy deployment plan and align all of your employees’ activities with company goals and objectives at each level of your business.
By establishing these types of KPIs or performance measures it will not only inform you how well your supply chain is doing, it will also help align the leadership team and all of the employees on what needs to be done to enable the achievement of the company’s goals and objectives.
As a result of you implementing a selection of well thought through leading and lagging Supply Chain measures, your customers will soon start to see your improvements having a positive impact, you will become more competitive and you will have the opportunity to become more responsive to your customer needs, command a premium for speed, lower your prices, improve profitability or increase market share.